Now that we have a firm understanding of the working of seepage and how it leads to piping, we will take a tour and assess further applications of filters. By now, you know the different types of drainpipes and dam filters at your disposal. Furthermore, you’re also able to determine which foundational drains work best for you. We have fully equipped you with the properties you need to consider as well as the requirements for each.
Drainpipes History
Dam management practices would begin to take a detour beginning in the year 1980. Then, there arose cries from different stakeholders as well as the public concerning the safety of embankment dams. As people awakened to this call, they started abandoning old drains and groutings! Older materials used throughout history would soon start to be replaced with newer technology. Whereas earlier constructions depended upon rigid drainpipes from clay and iron, newer models would enjoy relative flexibility from plastic. Even the previously used asbestos cement drainpipes would be classified as hazardous and their use discontinued.
Some factors that led to the poor conditioning of these ancient drainpipes include improper design, deterioration, damages on installation, and post-construction damage. That said, the integrity of drainpipes needs to be frequently evaluated during dam safety inspection using video examination. If there arises a need for modification, the damaged and poorly designed drainpipes should be done away with. But this is not always a feasible course of action. So what happens when plan B is called for?
Accessing existing drainpipes or getting cameras through them when the alignment is altered makes maintenance an extra job. On that same note, there are cases where replacement only removes some but not all drainpipes. In such cases, two methods will be used to combat drainpipes not fully removed. These are either slip lining or grouting. You will, however, need to follow through certain guidance.
Start by conducting a video examination on the interior of the draainpipes. This helps establish the specification requirements for the constructor. This should be done during construction. The foundation grain size distribution should then be determined. This enables calculation of the perforation size of replacement pipes. After this, the size of the replacement pipes including pipe thickness can be agreed upon. The next question to ask is how to get the replacement pipes in place. Should they be pushed (deadheaded) or pulled into place? Either way, a torpedo will come in handy to guide the liner through the existing pipe.
The other method – grouting – is placed using a slick line method. It functions by placing cement-based grout through the entire length of the existing pipe. A grout is never injected into the pipe but aims to fill it. When calculations indicate that the pipe volume exceeds the grout take, then there isn’t sufficient grout in the pipe. When lesser, there was an intrusion of grout into the foundation. The foundation should not be grouted. The grouting operations need to come before the foundation acceptance. This is then followed by the fill placement. Even with all this care and maintenance, internal erosion failure is still highly likely to occur.
The Addition of Dam Filters Protection
Conduits on the soil foundations will usually require filter protection. The whole conduits need to be backed up with filters and not just the sides and the top. The method of filter placement under the entire conduit structures need to be reliable. Any gaps present or low-density area will alternatively render the whole protection useless. A part of the conduit should be removed and reconstructed after placing the filters. This enhances intimate contact between the bottom of the conduit and the filters.
As previously seen, the most desirable filter placement position around conduits is closer to the centerline of the dam. This enables a greater overburden stress birthing greater confining stress thus keeping the filters intact. It also results in higher hydraulic resistance. That notwithstanding, the protective filters can also be located near the downstream. The problem with center placement is that a significant portion of the dam will need to be removed. This hinders the normal operation of the reservoir. Acceptable construction methods may also be used to diaphragm filters in the downstream locations. A good example would be placing stability berms downstream.
To consider the minimum dimensions for the addition of the filters, just consider the conduit size and the availability of seepage collars. FEMA has given out the guidelines for the minimum dimensions in both scenarios. However, the rules are based on the maximum/outside structural dimensions.
Geotextiles in Embankment Dams
Policies vary when it comes to using geotextiles in construction and rehabilitation. In some countries, the use of geotextiles will be limited to the ease of accessing repair and replacement. Also, it is restricted in instances when the dam safety is not entirely dependent on the use of geotextiles. Their reliability is uncertain because they are prone to clogging and installation damage. Therefore, interior areas that aren’t easily accessible for replacement as well as those areas that are critical to safety are discouraged from using them.
The use of geotextiles is quite limited, unlike sand and gravel filters that have been in use for years. Characteristics of sand filters are contrasted with geotextile characteristics to assess which has a higher performance rate. Sand and gravel mixtures are cohesionless materials. When the binder material is lacking or in short supply, a positive pressure is created as it flows to a soil boundary. The boundary then acts as the barrier for sand as it is compacted in a zone or trench.
Geotextiles, on the other hand, fail to apply positive pressure. It is only a flexible fabric that needs to be substituted with another material downstream thereby holding it against discharge face. These materials on the downstream also require some form of configuration to create similarities with the sand filter contact points. These materials fail to offer the needed support at the discharge face. The distance between contact points is also extended thus failing to protect against soil particle detachment.
In dams where geotextiles have been successfully applied, no instrumentation to check the gradients have been used. The only evidence for their superior performance is thus that which can be visually seen on the surface. The risks of piping remain which takes years to manifest on the surface. That said, using geotextiles on lower gradients may result in more success than on higher gradients. This is not to say that they prevent the detachment of soil particles at the soil interface. This is the case when critical gradients are exceeded.
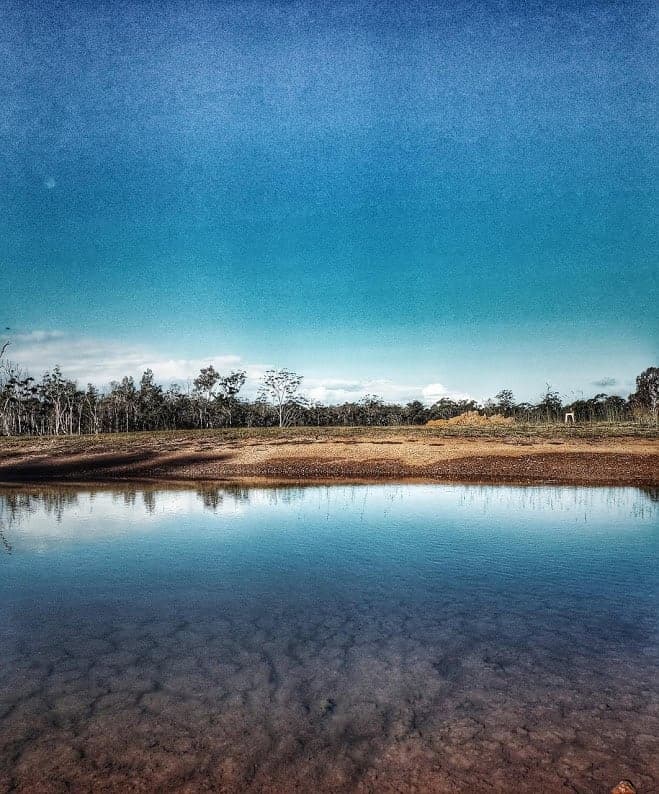
Historical Use of Geotextiles
In the past, geotextiles functioned as a separator between the coarser fill and the sand filter. The sand filter should be well designed however to ensure the geotextiles are not clogged. In other words, the soil fines should not reach the geotextiles. When placed in this position of two dissimilar soils, it will act as a separator. It prevents different materials from mixing up. It should never be used as a filter or drainage. Extra care should be taken to ensure fines do not access the filter as they will ultimately clog the geotextiles. Due to these complexities, dam owners are not recommended to use geotextiles.
Even in cases where the potential for high gradients is low, geotextiles are still not recommended. It has its associated difficulties including estimating the critical gradient and determining the gradient at the drain. Even in trenches where it has been successfully applied, it is important to note that the gradient isn’t high enough to cause soil detachment. The best dam practices would be to completely avoid using geotextiles to avoid enjoying the delusion that no damage is happening.
Alternatively, if the dam owner feels the necessity of using geotextiles, it should be applied in the non-critical areas of the dam. This greatly minimizes the risks involved. The dam owners should also conduct regular checks and maintenance of their structures. Existing drains should only be abandoned at the peril of the owners. Otherwise, they should be sealed to prevent foreign materials from eroding the poorly constructed drains. When undertaking the sealing, the method used should not introduce contaminants to new or existing drains.
Even when geotextiles are used under a riprap, effectiveness rarely improves. Not only does it thus become wastage of time but also of much-needed resources. The best alternative to work in most situations is the application of toe drains. But the purpose of its use depends on the engineer in question and the needs of the owner.
We have already seen that the safety of the dam is the key factor in the construction of earthen embankments. Every other factor is secondary to this. That said, the cost factor has made many constructors undermine safety. This fails to serve the purpose for which the embankment was constructed. It is a sound idea to seek multiple advice before constructing a dam. With all the discussed materials and designs, the owner has a bigger picture of what he should expect and what to aim for.
Moreover, the owner should base that decision on the requirements, size, and purpose of the dam. At the end of the day, you might use much more during maintenance due to a failure of observing detail during the primary construction. We will next seek to understand the applicability of these designs as can be seen in lab tests.
Pingback: Understanding Superabsorbent Polymers: Why They Fall Short In Dam Sealing | Big Ditch Dam Building Company